Buy American Act vs. Buy America Act: What’s the Difference?
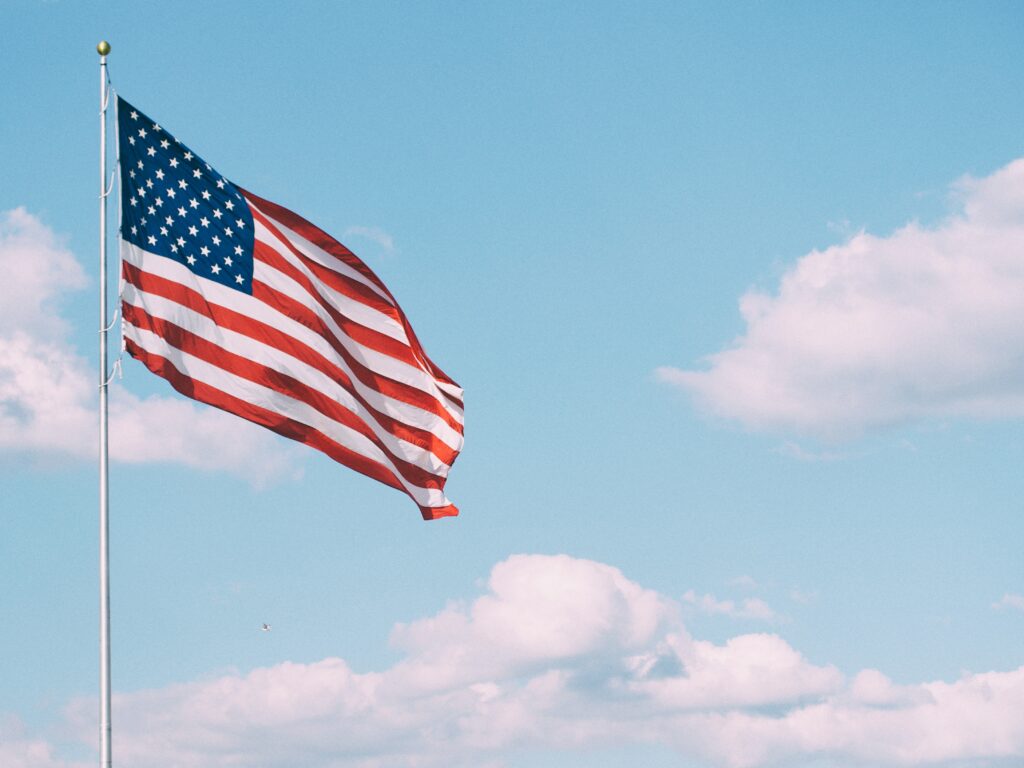
Sometimes one letter can make a big difference.
There have been plenty of times in our nation’s history when the government has decided to get a little creative with the names of important legislation. However, in the case of the Buy America Act and the almost-the-exact-same Buy American Act, this was apparently not one of those times.
As a result, we have pieces of legislation that sound very similar but are somewhat different once you dig into the details a little more.
The Buy American Act and Buy America Act are separated by nearly 50 years but are rooted in the same meaning. Both dictate that projects requiring federal funding must use products manufactured in the United States from primarily American materials. If that can’t be done, or if the cost is prohibitive, then waiver requests are allowed to swap American materials for foreign-produced goods.
While the two acts look and sound similar, there are distinctions. Failing to adhere to the regulations outlined in each could lead to massive fines for companies using federal dollars to get work done.
The Buy American Act
The Buy American Act was signed into law in 1933 at the height of the Great Depression to encourage the use of more American goods for government contracts.
Federal agencies and companies fulfilling contracts on their behalf are required to procure domestic products and construction materials for use when the contract is worth more than $10,000. To qualify, finished goods and materials must meet a few conditions:
- The materials must be intended for public use and in the public interest.
- Products or materials must be manufactured in the United States, and the cost of the mined or sourced components needs to account for at least 55% of the total cost of components, or…
- The product is available commercially off the shelf in a high enough quantity and quality.
If the materials needed to fulfill the contract are unmanufactured, they must be mined or produced within the U.S.
Waivers are available when domestic products are cost-prohibitive or if they could possibly run the U.S. afoul of a country we have a trade agreement. In cases like these, products can be replaced with those that are 100% grown, produced, or manufactured in another designated country.
Products can also include materials from non-designated countries, as long as they are manufactured in a designated country.
Buy America Provisions
Here is where things get a little tricky. Despite having almost the same name, the Buy America provisions are more specific in their rules.
Buy America is tied to federal assistance and generally related to infrastructure projects like highways, public transport airports, and even Amtrak contracts. It also extends into water infrastructure projects, though the contracts are generally covered by the EPA. Projects associated with Buy America are often tied to state and local transit, and water projects are headed up by the EPA.
In addition to only covering specific types of projects, Buy America goes one step further by allowing each federal agency to create its own requirements. This means the EPA, Federal Highway Administration, Department of Energy, and others have their own criteria to enforce and maintain.
As with the Buy American Act, Buy America has waivers available. They can be issued by the agencies on a case-by-case basis if the applications are inconsistent with the public interest or if there isn’t enough product available of a high enough quality.
Because rules and regulations can vary between agencies, it’s critical to work closely with the funding agency to fully understand what criteria need to be met. Staying within the rules helps avoid costly compliance issues and other mishaps.
Complying with Buy America
For products and materials to comply, they must be 100% manufactured in the United States. Additionally, the steel and iron used must be mined, processed, and manufactured in the U.S., meaning all components come from America.
It should be noted that the provisions allow for some different criteria based on the agency. For example, the FTA may require iron and steel to be 70% domestic product, but all manufacturing must take place in the U.S. Other agencies may lower the percentage to 50%, while the EPA and Federal Highway Administration are strict about iron and steel products being 100% U.S.-made.
Once again, it’s worth checking in with the agency providing the funding to learn more about the thresholds when Buy America provisions kick in and to what extent.
Build America, Buy America Act
The Build American, Buy American Act (BABA) was included as part of the Infrastructure Investment and Jobs Act of November 2021 and took effect in May 2022.
These rules expand the Buy America rules and stretch into other infrastructure projects besides transportation, including:
- Electrical utilities
- Transmission facilities
- Broadband operations
- Buildings
Besides expanding the industries where Buy America rules take effect, the requirements also expand beyond iron and steel to include nonferrous metals, including copper, plastics and polymer-based materials, glass and optical fiber, lumber, and even drywall.
Though the list has grown to include more materials, certain mined products like cement and stone are not included in the Build America, Buy America Act.
Like previous legislation, BABA has similar requirement thresholds that must be met, including items and construction materials produced in the United States. Qualifying projects also include any new construction, along with repairs and other maintenance to be done.
Waivers under BABA are available if the application goes against the public interest, materials aren’t available in the U.S. at the quality or quality needed, or if the price for U.S.-made products would raise the overall project cost by more than 25%.
Once a waiver is submitted, it undergoes review by the agency funding the project. It is also published, opening it up for a general public comment period lasting at least 15 days.
The Importance of American-Made Products
When compliance means everything, knowing where your products are made can make all the difference.
Sun-Pull’s products are all proudly made-to-order in the USA at our Rome, NY facility, then shipped quickly and accurately to distributors and job sites across the United States.
When location matters, Sun-Pull is ready with the wire and cable solutions needed to get the job done.